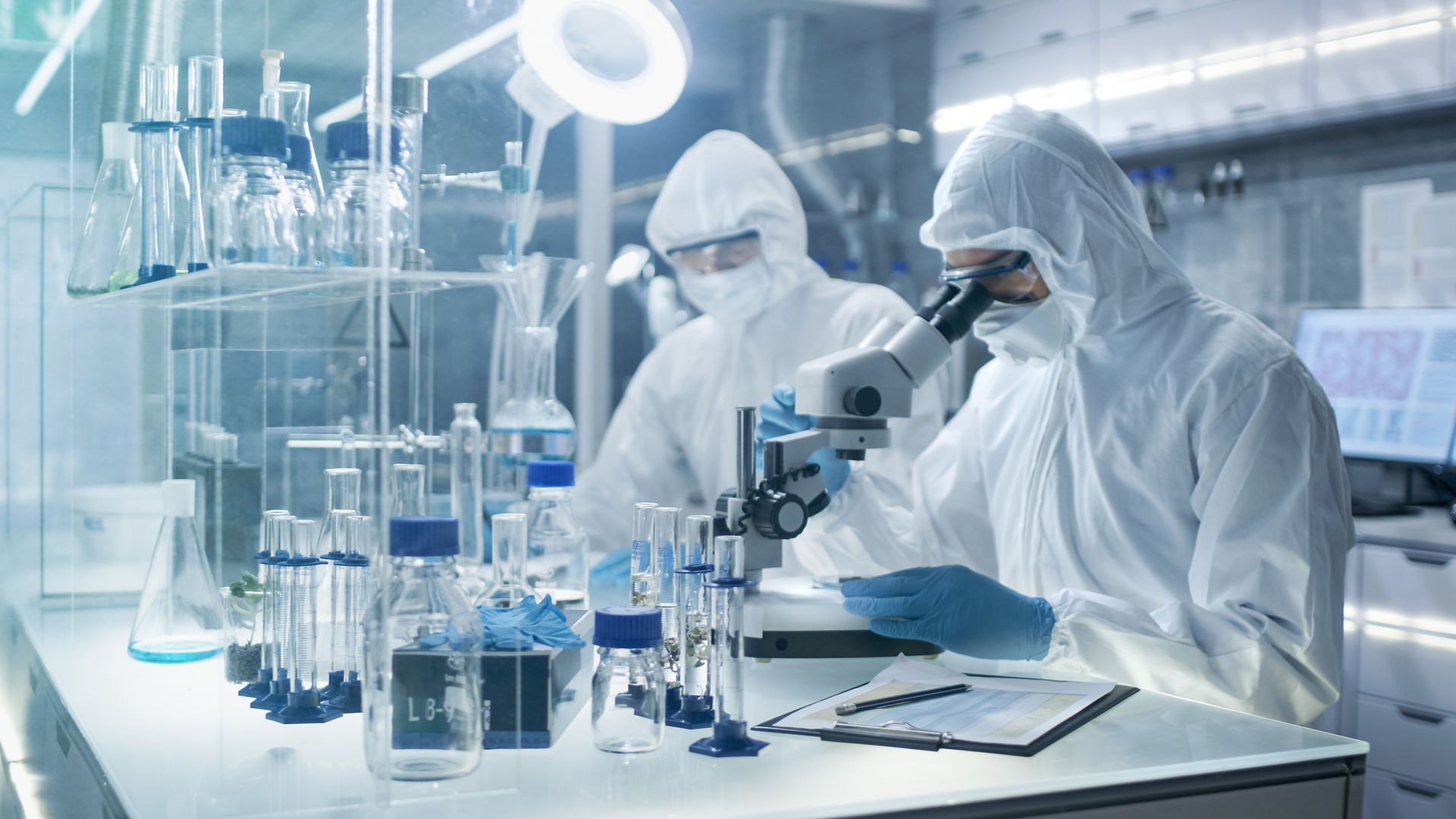

Advantages of PAN carbonization to produce Carbon Nanofiber
When it comes to producing carbon nanofibers, PAN carbonization offers numerous advantages over traditional production methods such as chemical vapor deposition (CVD). The electrospinning and subsequent carbonization process allows for finer control of various production parameters, resulting in several improved carbon nanofiber properties. The advantages of processing electrospun PAN into carbon nanofiber include:
High Aspect Ratio
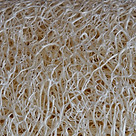
Electrospinning produces nanofibers with a high aspect ratio, meaning they have a much greater length compared to their diameter. This high aspect ratio is advantageous for applications requiring reinforcement or enhanced mechanical properties, as well as for providing a large surface area for functionalization or adsorption purposes.
Fine Fiber Diameter Control

Electrospinning enables precise control over the diameter of the nanofibers produced. The fiber diameter can be adjusted by modifying the electrospinning parameters such as polymer concentration, applied voltage, solution flow rate, and distance between the spinneret and collector. This control over diameter is crucial as it directly affects the properties of the resulting carbon nanofibers, such as surface area, porosity, and mechanical strength.
Versatile and Scalable
Continuous and Uniform Structure
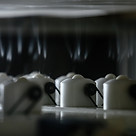
Electrospinning is a versatile technique that can be used to produce nanofibers from a wide range of polymers, including carbon precursors like polyacrylonitrile (PAN). It offers a high degree of flexibility in terms of material selection, allowing for tailoring of properties. Additionally, electrospinning can be easily scaled up for mass production, making it suitable for industrial applications.
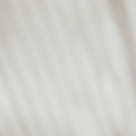
Electrospinning allows for the continuous production of nanofibers with a uniform structure. The process generates a steady and continuous jet of polymer solution, resulting in a seamless and interconnected nanofiber network. This uniformity is desirable for applications requiring consistent properties across the material.
Ease of Incorporation

Electrospinning allows for easy incorporation of various additives, such as nanoparticles, carbon nanotubes, or functional groups, into the nanofibers during the electrospinning process. This capability enables the production of hybrid nanofibers with tailored properties and functionalities.
Fiber Alignment and Orientation

Electrospinning can produce aligned or patterned nanofiber structures by using specific collector designs or applying external electric or magnetic fields. This capability is beneficial for applications that require anisotropic properties.
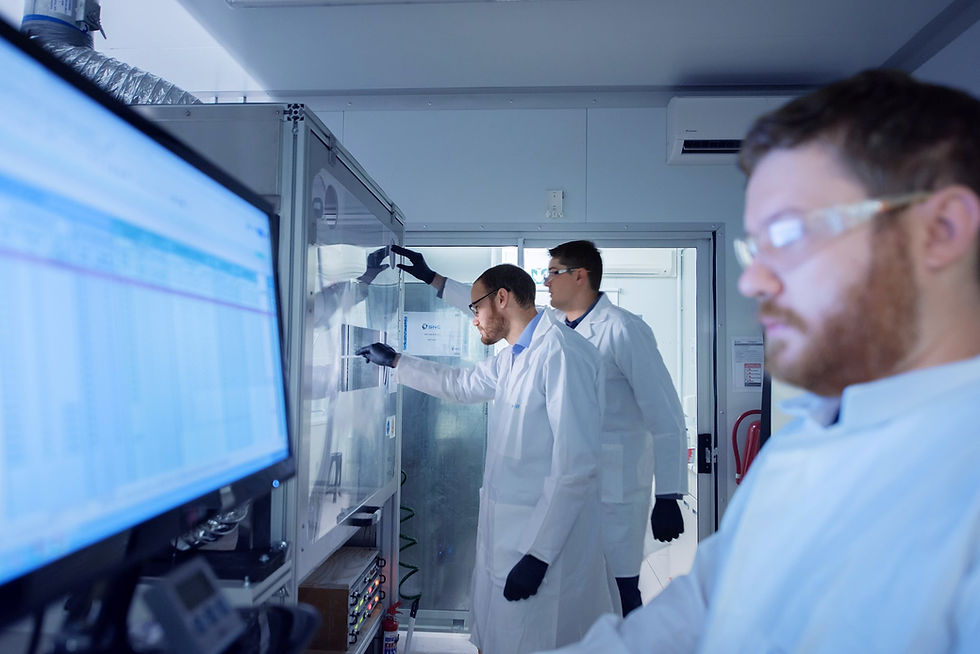
Production Technique -
PAN to Carbon Nanofiber
Carbon nanofibers can be derived from polyacrylonitrile (PAN) nanofibers through a process called carbonization.
A general overview of PAN carbonization is described below:
Polyacrylonitrile (PAN) is synthesized through a polymerization reaction using acrylonitrile monomers.
Polymerization
Electrospinning
The PAN polymer solution is electrospun with SNC BEST® to produce PAN nanofibers with the desired properties(i.e. fiber diameter, fiber alignment etc.) as required by the ultimate application of the CNF.
Stabilization
Carbonization
The PAN nanofibers are subjected to a stabilization process. Stabilization is typically carried out in air at elevated temperatures, typically between 200-300°C. During this process, the PAN nanofibers undergo chemical and structural changes, cross-linking and cyclization reactions, to form a thermally stable precursor.
After stabilization, the precursor nanofibers are further heated in an inert atmosphere, such as nitrogen or argon, at high temperatures, typically between 800-1500°C. This process is known as carbonization. During carbonization, the remaining organic components in the precursor are pyrolyzed, leaving behind a network of carbon atoms. The carbon atoms rearrange themselves into a graphitic structure, resulting in the formation of carbon nanofibers.
Post-processing
Depending on the desired properties, the carbon nanofibers can undergo additional post-processing steps, such as surface treatment, doping, or purification, to enhance their structural integrity, electrical conductivity, or other specific characteristics.